Specifying solid surface in today’s commercial construction doesn’t have to be difficult. Many architects/designers will rely on products they have used in the past. These specifiers are the conservative group and usually have been in their career for many years. More and more of today’s architects/designers are willing to use new products, green products and even experimental products. Both groups are now starting to understand that solid surface can be used for much more than just countertops. Solid surface is being used for everything from staircases/hand railings to outdoor seating. It doesn’t matter which group specifiers are in, they are all worried about one thing: price.
Problems can cost time and material. There are many problems that you can run into if you have never specified a solid surface color, pattern, shape, size or material. Problems that you may run into with patterns are seaming. Solid surfaces come in sheets. If the dimensions of your project are larger than the sheet, you will have a seam. If there is a pattern in the solid surface you have specified, there is a good chance you will see the seam. Solid colors in solid surface typically show no seam. A problem that you may encounter with shape is knowing which fabricator has the experience to thermoform and CNC the desired shapes for your project. Problems that you may experience with different types of solid surface materials are the restraints of the chemical makeup. Acrylics are great for back-lighted projects and are bad if it is extruded and has to be joined. No specifier wants to take on a project where the design calls for an eyesore of a seam which will be the first thing noticed. No specifier would want to take on a project where the size and dimensions have weight that cannot be managed.
At ASST we have 20 years of experience working with solid surfaces. We know just how tight a radius can be with different materials. We know how to hide the seam of a patterned material. We know that the weight for materials made of acrylic polymer and alumina trihydrate is approximately 4.5 pounds per square foot at ½” thickness (yes, that is important). At ASST, we know how to be specific with solid surface and we can help specify projects.
If you want to be specific about your next solid surface project, let ASST help you with your specifications. Whatever you need, ASST can build it to your exact specifications, in a safe manner, and to the quality standards you expect. Contact us now online or call us at 717-630-1251.
Most companies will tell you that loyal employees are their most important asset. What does that mean? How does a company keep the employees engaged in their job, feel valued and keep the company going in a positive direction? When employees are engaged and feel valued it shows in the quality of their work.
Many employers today view their employees as overhead. Some organizations see employees as a line item on the accounting spreadsheet, somewhere between cleaning supplies and fuel expense. Employees that don’t feel valued or engaged will always perform at a lower level. The cost of letting employees know they are valued and keeping them engaged compared to unhappy employees is minimal. Disengaged employees are less innovative, discontented, less productive and more likely to leave. High rates of employee turnover can be costly especially when it comes to training. According to Entrepreneur.com unhappy workers cost the U.S. up to $550 Billion annually.
At ASST we value our employees. We show our workers this by promoting and nourishing professional development, providing lunch for our monthly safety meeting, sharing stories/pictures of high profile jobs and sometimes just a “hey nice job”. Our management staff is not afraid to make some dust, often will help out in our fabrication facility an even help do installation. At ASST our employees are our most valuable asset. They know it and it shows in the quality of our solid surface fabrication.
If you want your next solid surface project to stand out from the rest, let our employees fabricate it for you. Whatever you need, ASST can build it to your exact specifications, in a safe manner, and to the quality standards you expect. Contact us now online or call us at 717-630-1251.
The healthcare industry has long understood the necessity of reducing the spread of bacteria by minimizing the use of porous materials. For years the healthcare industry has utilized Plastic Laminate (PLAM) casework because of the cost effective traits. Solid surfaces such as Corian ®, Durasein ®, Krion ®, LG HI-MACS ® and Avonite ® may cost more upfront; however, this material is virtually future proof.
Casework has traditionally been made of Plastic Laminate clad MDF with PVC glued to the edges. Some of the shortcomings of PLAM casework is the lifespan before adhesives start to fail, the durability of laminate materials and the lack of positive aesthetics. Once the casework is damaged or begins to come apart, it is no longer suitable for healthcare without the risk of harboring bacteria. No health system wants to find out that the loose PVC edging on a piece of casework is spreading bacteria. PLAM is traditionally made using square or rectangular shapes which limits the creativity of design. Today health systems are looking to assist people with ailments as well as being known as a leader in design.
Solid surface material is ideal for the healthcare industry. Solid surfaces are non-porous making it resistant to bacteria growth. Solid surfaces are easy to clean and because there are no layers, it will not separate. Solid surface is easy to repair, long lasting and can be thermoformed into any shape. At ASST, we have 20 years of experience fabricating casework for the healthcare industry. If you want to reduce the risk of spreading bacteria and wow your customers with the design, solid surface is the obvious choice.
If you want your next project to stand the test of time and “wow” your customer, let ASST help you out. Whatever you need, ASST can build it to your exact specifications, in a safe manner, and to the quality standards you expect. Contact us now online or call us at 717-630-1251.
The period of 2013 to today has brought many exciting and challenging opportunities for ASST. Large solid surface spiral staircases, thermoformed ribbon wall features and unique exhibit booth fabrications continue to stretch ASST’s experience and capabilities.
We look forward to Going Beyond™ with you for the next twenty!
Over the past three months we have rewound the past with some highlights of our history to date. Below are highlights from the most recent five years:
A considerable part of fabricating with solid surface is adhering separate pieces together. The solid surface fabrication joint requires a strong bond while maintaining aesthetics. This is accomplished by using the right solid surface adhesive that is matched to the surface color. The solid surface adhesive can be stronger than the material itself and with color matching, it is possible for the joint to subsist unnoticed.
Solid surfaces such as Corian©, Avonite©, Krion©, LG HI-MACS©, etcetera require adhesive to be joined together. Incorrectly joined solid surface can be unappealing and even dangerous. In most cases, designers and architects do not want seams that are visible for their projects. In all cases designers, architects and contractors want solid surfaces that will not come apart. Imagine someone leaning against a solid surface top and it coming apart. No one wants a product that could injure a customer.
Each manufacturer of solid surface makes adhesive that is color matching and ASST uses the correct color matching adhesive for each project. ASST has 20 years of solid surface fabrication experience. We know what adhesives to use, the correct amount to use and the correct way to finish the adhesive.
If you want your next project to stick in the minds of your customers, let ASST help you out. Whatever you need, ASST can build it to your exact specifications, in a safe manner, and to the quality standards you expect. Contact us now online or call us at 717-630-1251.
With the environment continuing to be a focus in the news, design professionals are required by end users to specify materials that are environmentally friendly. Carbon emissions generated from building products are a tremendous challenge for manufacturers across the globe. Specifying casework fabricated with woodbased products that are not only recycled, but also contribute to a lower carbon footprint is the end goal.
Many casework manufacturers utilize formaldehyde wood fiber particleboard for casework construction. These manufacturers tend to “downplay” their material construction in favor of a better price point. Laminates are usually not Greenguard certified and may contribute to off gassing. Specifying casework products without the proper green project credentials will likely prevent opportunities for LEED participation towards the fulfillment of point requirements.
To minimize the above issues, ASST has now partnered with TMI Systems as a dealer for their line of casework. Based in North Dakota, TMI is a leader in high quality plastic laminate modular casework fabrication. Their commitment to sustainability is impressive. With Single Chain of Custody certification from the Rainforest Alliance, TMI can provide a sustainable casework solution. Their modular casework products feature railmounted overhead cabinets and forward-thinking reconfigurable base cabinets. With Autodesk 3D BIM software, design professionals are able to more thoroughly document planning decisions in drawings used in the approval process. With cutting edge computer 3D renderings, end users can understand the proposed designs even better. With the new TMI/ASST alliance, design professionals are providing solutions that can truly evolve with end user needs.
Let us assist you with your next casework project! Whatever you need, ASST can build it to your exact specifications, in a safe manner, and to the quality standards you expect. Contact us now online or call us at 717-630-1251.
How do you design and shape solid surface projects? The technique of thermoforming is used to mold and shape different solid surface materials. This allows flat sheets of synthetic solid surface material to be transformed into almost any shape. By using heat and pressure the synthetic material is shaped into different three dimensional, rounded designs. The material is heated until it is pliable, placed over a mold and vacuum formed by removing the air between the material and a high temperature silicon membrane. Once the material has cooled it is trimmed to exact specifications using our 5 axis CNC.
Not all surfaces can be molded and turned into three dimensional shapes but most synthetic solid surfaces can. This process cannot be used on other solid surface materials like quartz and granite. Companies that choose synthetic solid surfaces have a broader range of artistic ability when it comes to solid surface projects. Thermoforming is a tricky trade and creating the right balance of heat and bend is crucial to this process. The different chemical makeup of synthetic solid surfaces requires different temperatures. There are also limitations of the bend radius with different materials. No one enjoys telling a customer that the project has to be redesigned because the material specified cannot be formed into the desired shape.
ASST has thermoformed most synthetic solid surfaces and we know the requirements for each. With the high level of technology in our fabrication facility, there are no limitations to the design of synthetic solid surfaces. ASST can bend synthetic surfaces any which way to bring your 2D project plans into to the 3D world.
Let ASST bend over backwards for you on your next project. Whatever you need, ASST can build it to your exact specifications, in a safe manner, and to the finest quality standards you expect. Contact us now online or call us at 717-630-1251.
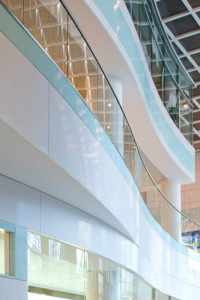
United Therapeutics
SOLID SURFACE IS REACHING NEW HEIGHTS. These Corian® and 3Form® walls were fabricated for United Therapeutics.
At ASST we are going Beyond the Surface Level™. CONTACT US TODAY FOR YOUR NEXT VERTICAL SOLID SURFACE PROJECT.
How do you get the ‘WOW’ factor across in your next solid surface project? Backlighting. Solid surface designs can be extraordinary and lighting them up can make them stand out from the rest. Backlighting acts like the cherry on top to the solid surface sundae and is a perfect finishing touch. The right type of lighting will make the architecture attract attention, illuminate details, and add dimension to the project.
Composition and depth of the solid surface can get lost in dark locations. Some of the leading solid surfaces on the market today have an element of translucency. The last thing anyone would want would be for that trait of translucency to go unnoticed. Don’t let your solid surface project fade into the background. Make it the centerpiece by lighting it up.
At ASST we create the most breathtaking and eye catching designs of Corian®, 3Form®, Krion®, LG HiMacs®, Avonite®, as well as other solid surface materials. Our creations come in different textures, colors, transparencies, and backlighting will make them stand out even more. Lighting fixtures can range from LED panels to light tape. Either way, lighting behind an ASST solid surface will make your project radiate in its space. ASST can design and incorporate backlighting into the solid surface project plan to make sure that it is unique and enhances the solid surface.
Let ASST guide you through the dark on your next solid surface backlighting project. Whatever you need, ASST can build it to your exact specifications, in a safe manner, and to the finest quality standards you expect. Contact us now online or call us at 717-630-1251.
The period of 2008 to 2012 witnessed even better project opportunities for ASST. Larger healthcare, education and important public projects such as the White House Visitor Center continued to help build ASST’s documented experience and capabilities.
We look forward to Going Beyond™ for the next twenty!
Over the next three months we will be rewinding the past with some highlights of our history to date. Below are the third five years: